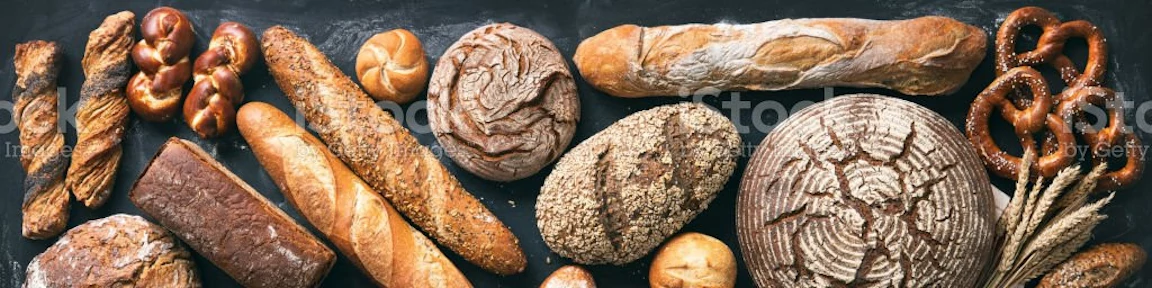
Luxury cookies take a few weeks
Bakery makes best use of Grant
Old Italian goes compostable
Rolling round and round isn't helpful
Organic butter in organic packaging
Confectionery Large and Small
Gas flush labels need gas flushing
Six pack robot makes it look easy
There are hundreds of applications we could showcase, but we prefer a simple website that's easy to use,
so here's just a representative sample.
Luxury cookies take a few weeks
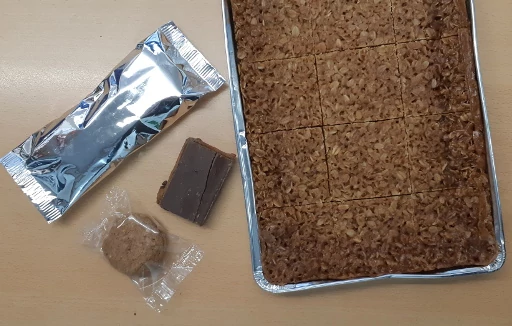
When a luxury cookie and cake supplier decided to bring its production and distribution facility under its own direct control it approached us for a cost effective and versatile flow-wrapper. In a matter of a few weeks we supplied a fully rebuilt, upgraded and adapted 'better than new' Ilapak Carrera 2000 complete with expert installation, training and full warranty.
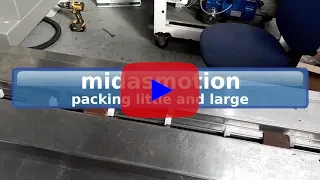
As well as our usual class leading multi-motor drive and control system we fitted our fully adjustable fold-box and a barrette system for transferring small products over a standard rotary jaw. This meant it could pack products as small as 50mm square up to 400 by 200mm trays with fast change-over and one fold-box.
Add in a used but late generation Markem-Image thermal transfer coder for automatic 'Best Before' printing and the cost saving compared with even a cheap 'entry level' new machine was significant. A Carrera 2000 model is Ilapak's higher-end model designed for continuous heavy duty operation and the cost of an equivalent new one can be two or three times as much.
Bakery makes best use of Grant
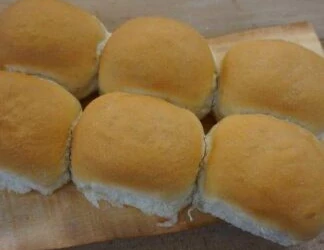
Stacey's Bakery of Ilkeston purchased one of our refurbished flow-wrappers using a government grant. This meant they could release labour from manual hand packing to help satisfy a large contract they had secured and still have plenty of grant money left over to invest in other areas of the business. A lot of small and medium size companies buy our equipment this way.
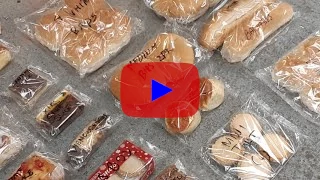
We often work with Portman Asset Finance and can arrange a competitive quotation but a lot of companies have their own preferred source of funding and we can also liaise directly with your bank, loan company or grant authority to make sure all the paperwork and details are correct and everything goes through painlessly.
Old Italian goes compostable
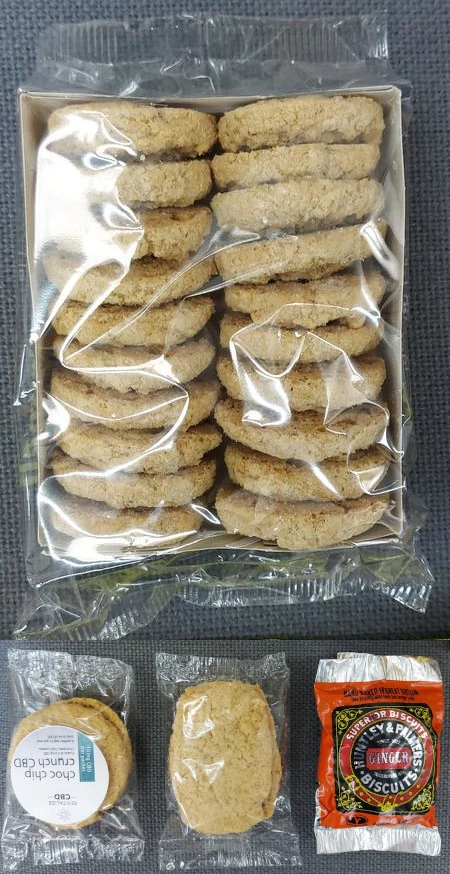
Lancashire Biscuits, part of Moorlands (UK) Ltd, came to us to extend the range of their Mondial flow-wrappers and, as part of the upgrade process, we added features, modifications and size-change parts that greatly extended the size range the machines can handle.
The flow-wrapper was an older Italian Mondial machine which, although fairly basic, was originally manufactured at a time when even entry-level machines were rugged and well engineered. We not only performed our usual upgrade and mechanical refurbishment but also added user adjustable jaw height, variable lug pitch and small product transfer rollers. This meant they could pack everything from a large tray of biscuits to individual and twin stacked biscuits of only 50mm diameter, in both standard OPP film and compostable NatureFlexTM.
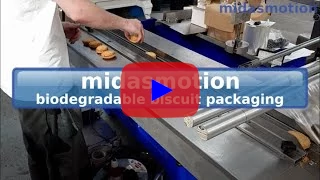
Some customers prefer adjustable fold-boxes and we can supply the correct type for each application, but in this case they wanted several fixed types which gave excellent quality tight packs and were easily changed over without requiring manual adjustment.
Rolling round and round isn't helpful
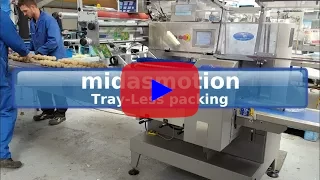
A supplier of pet foods was using a standard flow-wrapper for packing many different
products but when it came to round fat-balls they continually struggled. Round products
like these are notoriously difficult because they roll around inside the tube of film
which a standard rotary flow-wrapper relies upon to transport the product. We part
exchanged their existing well used Ilapak Carrera 500 machine for a larger fully refurbished
and upgraded Ilapak Carrera 1000 fitted with a specially developed powered top-brush.
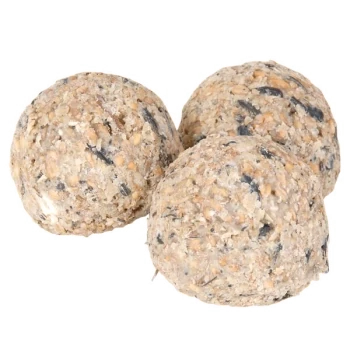
There are special machines available for handling difficult products such as this but they are very expensive and rare on the second hand market. Our solution was not only considerably lower cost but, like all our flow-wrappers, the internal upgrade meant changing products is fast and efficient with minimal change-over time and totally consistent results. The powered top brush holds the round fat-balls in position all the way through the machine but is easily removed, without tools, for products which don't require it.
Organic butter in organic packaging
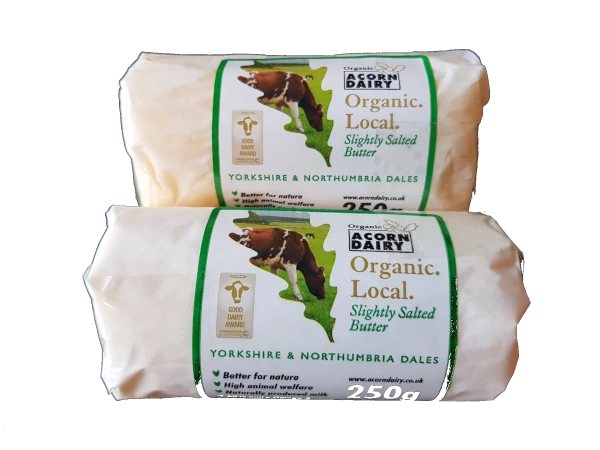
Acorn dairy are an award winning specialist producer of diary products and when sales of their organic butter took off they needed something faster and more efficient than the hand packing they were used to. We supplied an inverted 'top seal' flow wrapper in which the operators simply placed cylinders of butter onto a moving conveyor infeed without positioning lugs or other restrictions. The sticky butter is carried and supported through the machine rather than being pushed along a stationery deck.
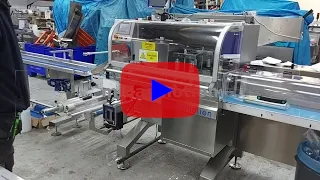
To go with their organic products they needed something other than plastic wrapping and we configured the machine to work with paper based wrapping material that is 100 percent home compostable.
The infeed system is specially designed fully from stainless steel with tool-less belt removal for easy routine cleaning.
Confectionery Large and Small
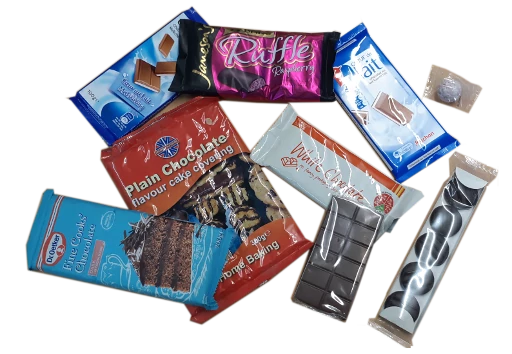
Some in the confectionery industry spend large amounts on fully automated high speed packing lines. At the other end of the scale specialist chocolatiers require a different approach and their priority is often versatility and low cost. Of course some of the requests from our customers are new and demanding and the challenge of providing an excellent solution, often based on standard flow-wrappers, requires ingenuity and experience in equal measure.
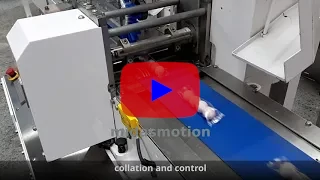
UK's largest producer of 'own brand' chocolate bars has three of our fast fully automated packing lines taking rows of products direct from the moulding machines, aligning, queuing and metering them into flow wrappers. The same lines handle small individual snack bars at very high speed all the way up to large catering slabs.
One of the largest producers of chocolate bars in France purchased two of our refurbished and upgraded flow-wrappers to pack its products. Both included automated in-line feeders.
On the other hand, the video also shows two fully refurbished flow-wrappers, upgraded and modified for small specialist chocolate producers. Configured to pack a wide range of products, from small round balls to chocolate bars in compostable film and including an integrated automatic card inserter and folder.
Gas flush labels need gas flushing
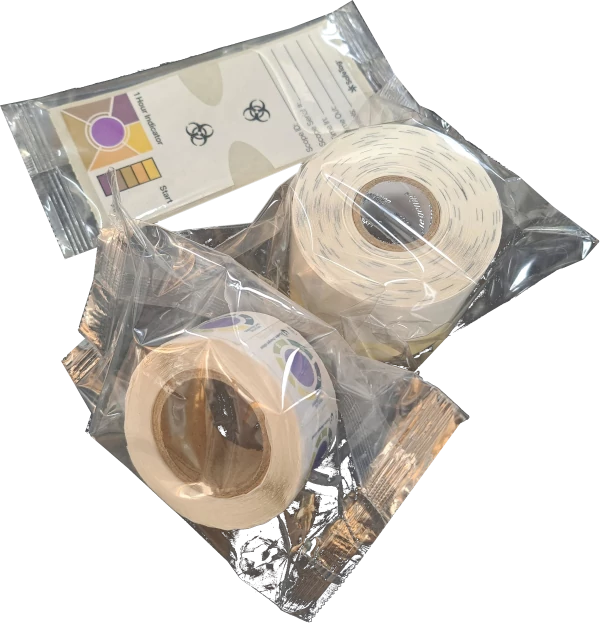
In many cases MAP (Modified Atmosphere Packaging) is an option that can extend the shelf life of your products, but in others it's an essential requirement. An unusual non-food application is the packaging of colour changing labels which need to be kept in inert gas filled packs until required, sometimes to warn of bad gas flushing!. We supplied a fully re-manufactured PFM Tornado long dwell 'D-cam' flow wrapper coupled to a custom built infeed with integrated loading shelf. The machine handled both thin individual labels and much thicker rolls of colour sensitive tape with fast and efficient change over including adjustable gas flushing lance and monitoring equipment.
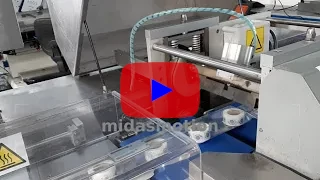
New flow wrappers capable of high integrity sealing for MAP and similar applications are more complex than standard rotary jaw flow wrappers and can be very expensive. We have supplied re-manufactured 'box motion' and 'D-cam' rotary jaw machines for food, non-food and pharmaceutical applications at a fraction of the cost of a new equivalent machines.
Six pack robot makes it look easy
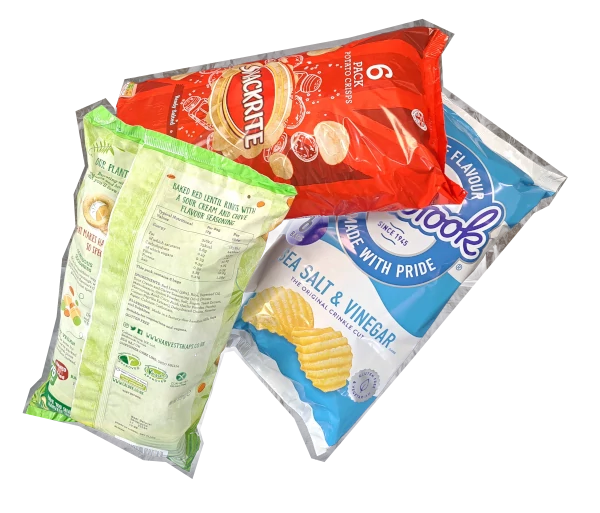
We have supplied both re-manufactured flow wrappers and refurbishment of customers own machines to some of the major crisp and snack food manufacturers in the UK and EU. Building up an inherently unstable stack of six crisp packs with inconsistent and variable shape and then passing them through a flow wrapper can be a difficult task. It requires careful machine configuration and special additions that come from a proper analytical approach, not to mention years of experience.
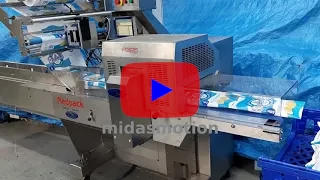
This is particularly true if the stack is built up in the moving infeed by robots with little or no human attendance. Such robotic systems are often complex but working closely with robotic engineers and having an adaptable and well developed robot interface makes a big difference to both the installation and commissioning process as well as the ongoing efficiency of the packing line.